Was ist Lean Management?
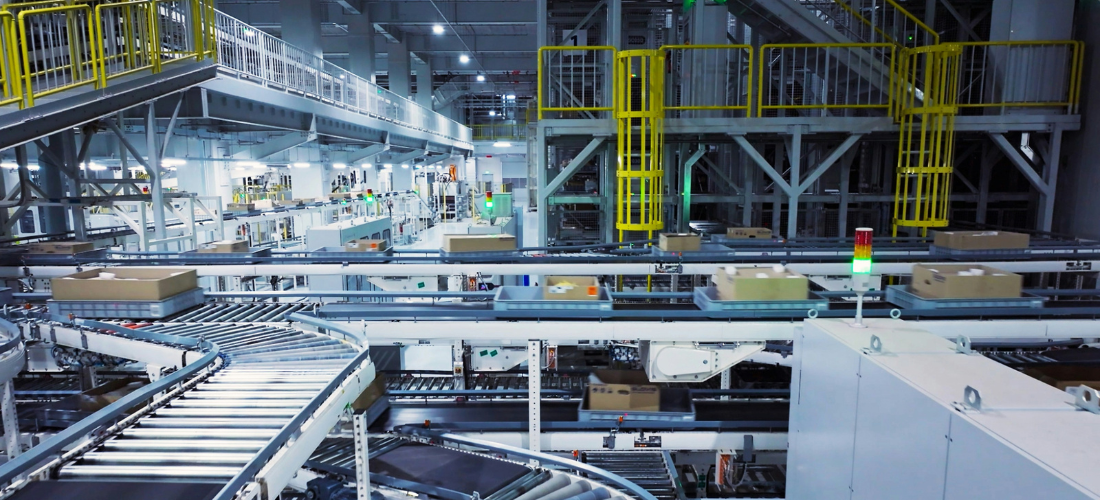
Lean Management beschreibt einen Ansatz, der darauf abzielt, Prozesse in Unternehmen effizienter zu gestalten, Verschwendung zu minimieren und gleichzeitig die Wertschöpfung für Kunden zu maximieren. Ursprünglich in der Produktion entwickelt, hat sich dieser Ansatz inzwischen in nahezu allen Unternehmensbereichen etabliert. Was Lean Management genau ist, welche Geschichte sich dahinter verbirgt und wie man diesen Ansatz etabliert, schauen wir uns in diesem Beitrag an.
Definition Lean Management
Lean Management ist ein strategischer Ansatz, der auf die Optimierung von Prozessen und die Vermeidung von Ressourcenverschwendung abzielt. Der Begriff „lean“ (englisch für „schlank“) bezieht sich auf den Fokus, nur die notwendigen Aktivitäten durchzuführen, die echten Mehrwert schaffen. Verschiedene Formen der Verschwendung, wie Überproduktion, Wartezeiten, unnötige Transporte, zu hohe Lagerbestände oder ineffiziente Arbeitsprozesse, sollen konsequent vermieden werden.
Die 5 zentralen Prinzipien des Lean Managements
- Wert aus Kundensicht definieren: Der Fokus liegt darauf, was der Kunde als wertschöpfend betrachtet.
- Wertstrom analysieren: Die Schritte in der Wertschöpfungskette werden auf Effizienz überprüft.
- Fluss herstellen: Arbeitsabläufe werden optimiert, um reibungslose Prozesse zu gewährleisten.
- Pull-System implementieren: Produkte oder Dienstleistungen werden nur auf Abruf gefertigt, um Überproduktion zu vermeiden.
- Kontinuierliche Verbesserung: Prozesse werden regelmäßig überprüft und verbessert.
Geschichte des Lean Managements
Join the map!
Werde Teil der größten Freelancing-Plattform im deutschsprachigen Raum.
Die Ursprünge des Lean Managements liegen in der Automobilindustrie. Der Ansatz wurde maßgeblich durch das Toyota-Produktionssystem (TPS) geprägt, das in den 1950er-Jahren von Taiichi Ohno und Eiji Toyoda entwickelt wurde. Ziel war es, eine Produktionsweise zu schaffen, die flexibel, effizient und ressourcenschonend arbeitet – im Gegensatz zu den damals verbreiteten Massenproduktionsmethoden in den USA.
Der Begriff „Lean“ selbst wurde jedoch erst 1990 durch die Veröffentlichung des Buches The Machine That Changed the World von James P. Womack, Daniel T. Jones und Daniel Roos populär. In dem Werk wurde Toyotas Ansatz als überlegenes Produktionssystem beschrieben, das nicht nur Kosten spart, sondern auch eine höhere Produktqualität liefert.
Heute wird Lean Management nicht mehr nur in der Fertigung eingesetzt, sondern findet Anwendung in unterschiedlichsten Bereichen wie Logistik, Softwareentwicklung, Dienstleistung und sogar im Gesundheitswesen.
Ziele des Lean Managements
DDas Hauptziel des Lean Managements besteht darin, einen optimalen Wert für den Kunden zu schaffen, während gleichzeitig die Ressourcen effizient genutzt werden. Die wichtigsten Ziele im Überblick:
- Verschwendungsreduktion: Durch die Eliminierung nicht-wertschöpfender Aktivitäten können Unternehmen Kosten senken und die Produktivität steigern.
- Qualitätsverbesserung: Fehler in Prozessen sollen frühzeitig erkannt und behoben werden, um eine hohe Kundenzufriedenheit zu gewährleisten.
- Flexibilität: Unternehmen sollen in der Lage sein, schneller auf veränderte Kundenbedürfnisse oder Marktbedingungen zu reagieren.
- Mitarbeitermotivation: Durch die Einbindung der Mitarbeiter in kontinuierliche Verbesserungsprozesse wird deren Engagement und Innovationsbereitschaft gefördert.
- Kundenorientierung: Der gesamte Fokus liegt darauf, Produkte oder Dienstleistungen anzubieten, die einen echten Mehrwert für den Kunden bieten.
Durch diese Ziele können Unternehmen Wettbewerbsvorteile erzielen und nachhaltiges Wachstum fördern.
Wo lässt sich Lean Management einsetzen?
Lean Management ist längst nicht mehr auf die Produktion beschränkt. Mittlerweile hat sich diese Philosophie in der Praxis von unterschiedlichsten Abteilungen und Branchen durchgesetzt. Zu den typischen Einsatzgebieten – neben der Produktion – gehören:
- Logistik und Supply-Chain-Management
- Verwaltung und Backoffice
- Dienstleistungssektor
- Produktentwicklung
- Softwareentwicklung
Woran kann Lean Management scheitern?
So schön der Gedanke von schlankeren und besseren Prozessen auch ist, es gibt einige Herausforderungen, an denen Lean Management scheitern kann. Zu den häufigsten Gründen zählt beispielsweise die mangelnde Unterstützung der Führungsebene. Wird die Philosophie von oben nicht gelebt, kann sie von unten nicht fruchtbar umgesetzt werden. Gründe sind außerdem:
- Mitarbeiter werden unzureichend geschult
- Unternehmen konzentrieren sich nur auf kurzfristige Einsparungen
- Die gesunde Basis in Form der Unternehmenskultur fehlt
- Wer sofortige Ergebnisse erwartet, wird aufgrund der Kontinuität scheitern
Um diese Herausforderungen zu überwinden, ist es wichtig, Lean Management strategisch und nachhaltig zu implementieren und die gesamte Organisation einzubeziehen.
Lean Management: mehr als Tools und Methoden
Die Lean-Philosophie zielt darauf ab, Probleme an die Oberfläche zu holen und sichtbar zu machen – anstatt sie zu verstecken. Doch wo Probleme identifiziert und analysiert werden, werden auch Fehler benannt, und wer gibt schon gerne Fehler zu? Dabei ist genau das der Kern von Lean Management: eine (Unternehmens-)Kultur zu schaffen, die Fehler nicht verurteilt, sondern in ihnen – wie in erkannten Problemen – eine Chance sieht, sich weiterzuentwickeln und zu verbessern. So entsteht ein kontinuierlicher Verbesserungsprozess (KVP).
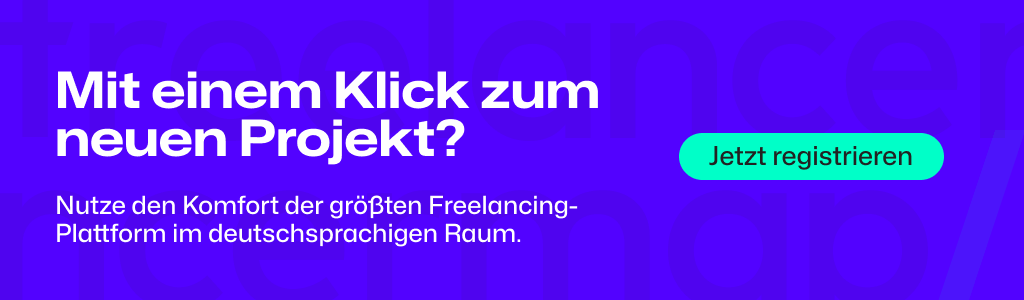